Cross Report: Pressure to specify untested flat roof systems
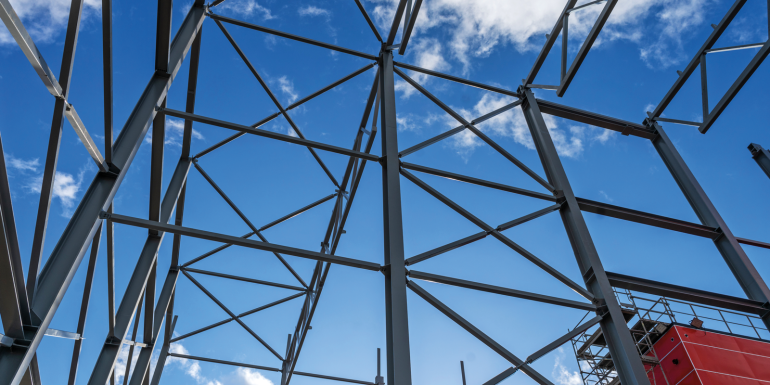
Collaborative reporting for safer structures. Report 1344: Collapse of concrete canopy over house entrance
A reporter provides details of the sudden collapse of a precast concrete canopy above their front doorway
The reporter has lived in the property for 15 years. They had complained to the local authority, their landlord, on numerous occasions about their concerns over cracked lintels and cracks in internal walls and ceilings. The collapse of the canopy above the front door has caused further concern about the overall safety of their home.
The reporter stated that the landlord’s representative, who attended the site, indicated that the house was safe and that the collapse of a canopy had not happened at any of their other properties. They noted they would provide a glass reinforced plastic canopy replacement. The reporter contacted CROSS after reading previous reports on canopy collapses.
Comments
The reporter is to be thanked for raising this. CROSS previously reported these concerns in 2009 in CROSS Safety Report 126: Precast concrete canopies in housing.
The collapse could have led to a serious injury or a fatality. The images supplied show the main reinforcement lower than it should be and its position is variable along its length; poor manufacturing control is likely to be a significant contributing factor. The root of the cantilever is particularly vulnerable as it is where the concrete is most likely to crack and is often where water gathers. Furthermore, the canopy waterproofing does not appear to be well bonded to the wall, allowing water to enter the top surface of the concrete, contributing to the corrosion of the reinforcement. A flashing detail, if present, might have inhibited water from entering.
Key learning outcomes
For building managers and building surveyors:
- be aware of the potential inherent defects associated with this form of precast concrete canopy
- do not ignore signs of cracking and corrosion, as they may be symptomatic of a significant defect. Engage a suitably qualified and experienced engineer to carry out a structural assessment and inspection; and
- all structures should be regularly inspected as part of a maintenance schedule.
The level of corrosion to the reinforcement indicates the concrete was likely fully carbonated or contained chlorides. Any cracking or signs of corrosion on the soffit are difficult to ascertain from the images and they may have been painted over at some point. The photographs of the other cracked lintels suggest that there is a generic degradation design issue and that the canopy failure was not just a one-off. Their condition warrants further investigation.
The report highlights that critical structural elements can contain defects that remain hidden for years until, eventually, they deteriorate to the point where they fail. Regular checks and maintenance should be undertaken on all structures and any evidence of corrosion or cracking should be investigated further.
The reported comments from the landlord’s representative do not inspire confidence. They should have immediately instigated an inspection of all similar properties and carried out repairs or replacement to prevent a recurrence of the incident elsewhere.
A criticism in the Grenfell Tower Public Inquiry Report was that the tenant management organisation consistently ignored tenants’ concerns.
Further reading
Further examples of CROSS Reports regarding incorrectly placed reinforcement in cantilevers coupled with long-term degradation include:
- CROSS Safety Report 341: Balcony collapse at block of flats: b.link/CROSSUK_341
- CROSS Safety Report 435: Balcony construction defects of residential flats: b.link/CROSSUK_435
- CROSS Safety Report 126: Precast concrete canopies in housing: b.link/CROSSUK_126
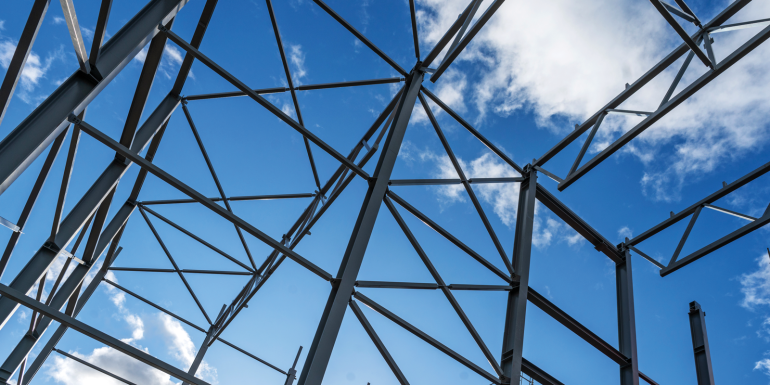
Report 1319: Pressure to specify untested flat roof systems
A reporter was asked to prioritise cost over safety in a quote
The reporter explains they were in the process of preparing a quote for a project that included two podium flat roofs and were specifying a roofing system that would meet the requirements of Approved Document B (ADB) and the BS EN 13501-5 BROOF(t4).
However, they were informed that the client was “desperate for a value-engineered option due to budget constraints” and that “it is a competitive market and client budgets are very tight now”. The reporter says they were advised to “give your best price straight away” and that it was made clear the BROOF(t4) test was not a requirement, but a modest price was.
The reporter believes that ADB is clear about the status of Test 4, highlighting that Volume 1 Appendix B clause B17 states: “BS EN 13501-5 refers to four separate roof tests. The suffix (t4) used in paragraph B16 indicates that Test 4 is to be used for the purposes of this Approved Document.”
The reporter also says designers and builders should follow guidance from trade associations such as the Liquid Roofing and Waterproofing Association, the Single-Ply Roofing Association and the Fire Protection Association. It could present life safety issues if there is a fire and people are on a podium roof constructed with untested products.
Comments
The panel notes that this is a building regulation matter. ADB and BS EN 13501-5 BROOF(t4) is only one way of satisfying compliance. Until March 2025, BS476-3 is also an alternative route for compliance. The overriding requirement is restricting external fire spread sufficiently to satisfy Building Regulations Part B4(2) of Schedule 1 to the Building Regulations 2010.
If a roof is not designed to meet the BROOF(t4) standard, an alternative method to demonstrate compliance with building regulations is necessary. However, in this instance, it seems the client was not seeking such equivalence but rather requesting that the reporter provide a roof that would fail to comply with Requirement B4(2).
This arguably reflects a prevalent issue in construction industry culture, prioritising cost over correctness, which is unacceptable. The ‘race to the bottom’ still presents a significant challenge within the industry and, unless it is addressed, such situations will continue to occur. Clients, designers, engineers, building control and other professionals must exhibit integrity and ensure compliance with established standards.
Building control clearly should not approve an installation that does not comply with building regulations. This may lead to remedial work being required, which would outweigh any cost savings. It is concerning however, that a client appears to believe they would be able to avoid complying with Requirement B4(2). Building control has a responsibility to undertake sufficient checks of designs and sites to prevent unscrupulous or incompetent practices.
There is nothing inherently wrong with cost efficiencies and value engineering, but it needs to be done with safety as a pre-requisite.
- See the Fire Protection Association’s Fire Safety of Balconies and Terraces at b.link/FPA_balconies
- To subscribe to the CROSS UK newsletter (structural and fire safety concerns), visit cross-safety.org/uk/user/register
Image credit | iStock