Apprentice’s project makes huge energy savings
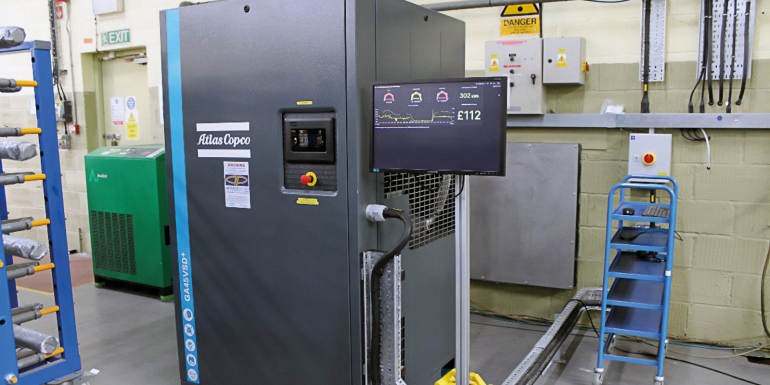
Paydon Blow’s project monitored energy usage across the compressed air system
What happens when an engineering apprentice identifies energy and cost savings for a company as part of their placement?
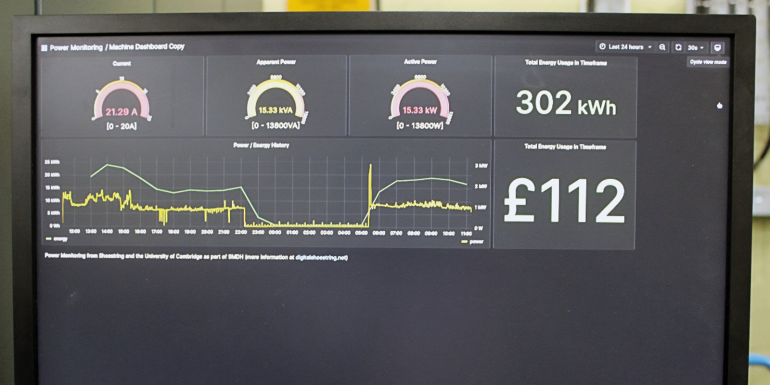
A student project by Trox engineering apprentice Paydon Blow has the potential to save the company up to £10,000 per year at its Thetford-based factory. Blow is studying engineering at West Suffolk College and needed to carry out a project in an active manufacturing environment for his course, using real-life commercial and financial criteria to determine impact.
After discussing the project’s scope with his industry mentor Roger Trueman, Trox Maintenance Manager, the company purchased the materials for the project. Blow wanted to explore energy-saving opportunities using the Raspberry Pi to measure, record and display energy consumption for this project. A Raspberry Pi is a low-cost computer that runs Linux. It provides a set of general-purpose input/output pins, which enables interaction with electrical components.
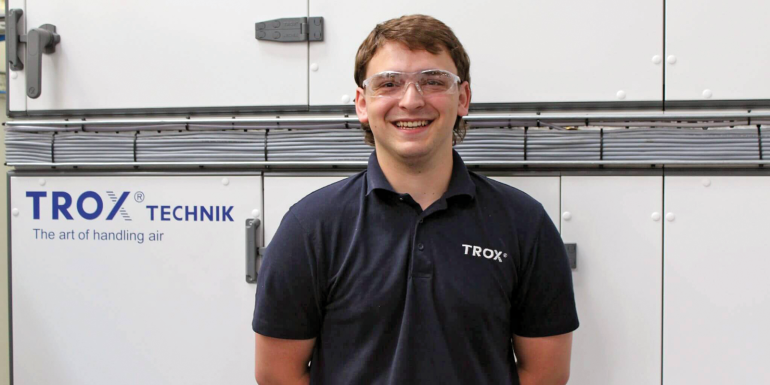
Monitoring air use
The aim of Blow’s project was to monitor energy usage across the compressed air system. The company had recently replaced four old air compressors with a single new one with advanced technology, which had already achieved significant cost reduction. The savings identified during this project were in addition to this.
Thanks to the project, Trox’s engineering team was better able to understand demand for compressed air around the factory, including times of day for most and least demand. This allowed certain machinery to be switched off when not in use to reduce energy consumption.
The project has reduced compressor operating hours by more than 10%, bringing an estimated saving of around £3,500 in energy costs per year. When operating at full scale, the cost savings could be in the region of £10,000 per year, exceeding the savings anticipated in the feasibility study.
“It has furthered my understanding of the importance of data gathering and using data to identify the areas where cost savings can be made,” says Blow. “I was also able to use this to build upon my portfolio of work for my apprenticeship.”
Trueman adds: “My only experience of Raspberry Pi prior to Paydon’s project was as a gift I gave to my nephew one Christmas. Seeing this extremely low-cost technology in action in a busy manufacturing environment however, has shown me that there is far more potential than I realised. We’ve already identified more machinery to monitor to make it easy for us to manage energy costs, and we’re looking at other solutions that could benefit our manufacturing operations.”
Neil Addison, Managing Director at Trox UK, says this highlights the mutual benefit of apprenticeships. “The combination of targeted on-the-job training and academic qualifications offered by apprenticeship programmes helps our industry sector to develop the skilled personnel necessary to tackle the sustainability challenges for the built environment of the future. We have seen so many of our apprentices move into successful careers within Trox after their apprenticeships and continue to be committed to this route into our industry.”
For more, visit troxuk.co.uk